Packaging is a broad category in the manufacturing industry. Different products necessitate different packaging options to be packaged securely and according to industry standards. Packaged cans have been so popular recently, that I’m sure you have used one at some point. The numerous advantages they offer users are the main reason for their popularity in different industries.
Each production line has its own set of requirements. You may prefer a specific sealing method, a higher output rate, or even a specific type of pouch coding. Today, we will focus on the types of packaging cans, the materials they are made of, their advantages and disadvantages, and their applications. Learn more.
Why Cans For Product Packaging
Convenience. Beverage cans are prized for their portability and convenience. They are great for active lifestyles – hiking, camping, and other outdoor excursions – because they are lightweight and robust and do not break easily. Cans are particularly ideal for usage in outdoor locations where glass bottles are prohibited, such as stadiums, concerts, and athletic events, allowing customers to enjoy their favorite beer whenever and wherever they want.
Protection of the product. Canned coffee beans rely heavily on taste and individuality, so protecting those qualities is crucial. Light and oxygen, two key enemies of coffee and many other products, can hurt flavor and freshness. Metal provides a powerful barrier against these two enemies. Cans have a greater surface area that allows you to advertise your brand with eye-catching images, capturing customer attention in the store.
Sustainability. Tin cans aren’t simply attractive; they are also a purchase that customers can feel good about. Metal packaging is recyclable, which simply means it can be reused without losing its performance or integrity. A well-recycled can return to the market in as little as 60 days.
Types Of Packaging Cans Based On Materials
Packaging is a vital concept in our daily lives; most companies and businesses have adopted it to boost their sales and attract new customers in their businesses. Packaging cans are based on different types of materials, and in this article, we will learn more about them. Read on.
Metal Cans
These are clean and empty metal containers mainly composed of aluminum, tin-plated steel, or zinc-plated steel that is commonly used for packaging food, beverages, or any other items and are devoid of food, beverage, or other contaminants, as defined by the Agency in the rules and regulations.
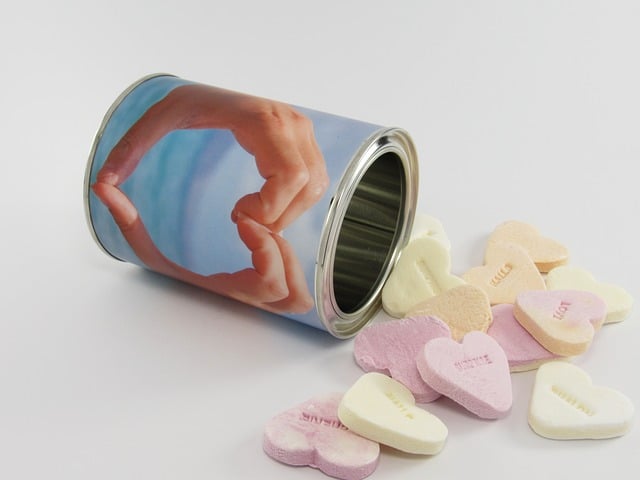
Advantages Of Metal Cans
- Outstanding mechanical qualities. Metal packaging containers are rigid and easy to handle, allowing them to withstand collisions, vibrations, and stacking. This makes them convenient for transportation and storage, extending the sales radius of goods.
- Outstanding barrier properties. Metal packaging containers may block not only gases like air, oxygen, water vapor, carbon dioxide, and so on, but also light, particularly ultraviolet light, preventing deliquescence, degradation, decay, and fading of the contents.
- Excellent thermal conductivity. The great efficiency of heating and cooling provided by food metal cans improves the effect of high-temperature sterilizing and rapid cooling, and the contents can be cooked.
- It is simple to use. The metal packaging container is durable and easy to transport. A lot of beverages and food cans nowadays have easy-open lids, which makes them more convenient to use and adapt to the fast-paced life of modern society. They are also widely used in tourist areas.
- High adaptability. Because of the metal’s ductility, it can be produced with great precision and speed for complex shaping procedures. A three-piece tinplate production line, for instance, can produce 360 cans every minute. Metal containers can cover a wide range of consumer demands at a cheaper cost because of their great products.
- Lovely decorating. Metal containers typically have a lovely metallic shine, which is complemented by vibrant graphic printing that enhances the product’s appeal. As a result, while delivering gifts, people frequently prefer to utilize metal containers.
- Disposable and simple to use. After they have been used up, metal containers may usually be recycled and repurposed. It not only recycles materials and saves energy, but it also reduces pollutants in the environment. Even if the rusted metal is distributed throughout the soil, it will have no negative impact on the ecosystem.
- Safety and hygiene. Metal containers fully meet the cleanliness and safety criteria for food containers due to the use of appropriate coatings.
Permeability to magnetic fields, Steel containers can be transported using magnetic force since they are magnetically permeable. This will make them the ideal packaging material for most products.
Disadvantages Of Metal Cans
Chemical composition. Under the influence of acid, alkali, salt, and humid air, it is prone to rust. This has narrowed the scope of its application. However, thanks to a range of good coatings, this disadvantage can now be overcome.
Poor economic conditions, like inflation. Metal can prices are quite higher than before. This deficiency is also being gradually addressed as a result of technological advancement.
Applications Of Metal Cans
- Beverage cans. Aluminum cans are commonly used to package soda, beer, and even wine.
- Food cans. Metal cans are commonly used to package vegetables, soups, fruits, pet food, and meats.
- Paint cans. Metal paint cans are still widely used in industries.
- Tube cans. Metal tubes, rather than plastic tubes, can be used to package lotions, toothpaste, and other viscous beauty goods.
Tin Cans
Tin cans are thin metal containers used for the delivery or storage of products. One of the most prevalent types of packaging is tin packaging. Food products such as soft drinks, soups, and seasonings should be packaged in this manner.
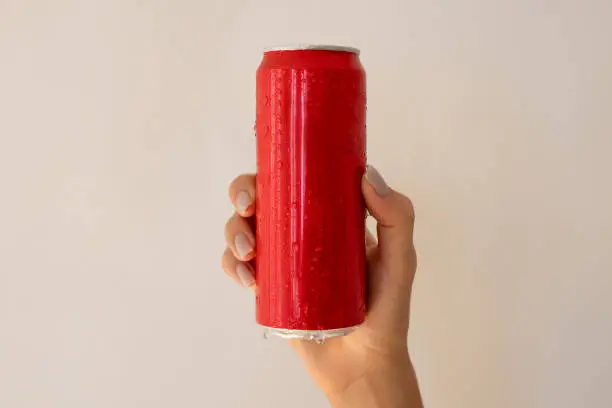
Advantages Of Tin Cans
- A Longer Shelf Life. Tin simply has a longer shelf life than other materials, such as steel and aluminum. It’s because of the tin substance, which doesn’t react with the food. Steel and aluminum, on the other hand, can easily corrode and even damage food depending on their acidity. Because other materials cannot be utilized to store medications, liquids, or soups, containers made of anything other than tin are used. Tin can packaging guarantees that the food lasts a long time and preserves its nutritional value.
- Handling is simple. Because tin cans are lightweight, you have surely noticed how easy they are to handle. When it comes to carrying packaged goods across great distances, weight is a major consideration. The majority of service providers charge a transportation fee based on the weight of the goods being transported. Anyone trying to lower production costs would look to reduce transportation expenses, which could only be done if a lightweight alternative existed. Tin cans are an excellent alternative that saves money on transportation.
- Rigid and strong. Tin cans, due to their strength and rigidity, provide a lot of flexibility in terms of packaging. These cans will retain their original shape even when subjected to a strong impact. Therefore, we can conclude that tin can packaging is the way to go for anyone who wants to prevent the problem of deformed cans and reduce any costs associated with stock returns. They enable the use of various modes of transportation while also ensuring that they can remain in good condition until they reach the final user.
- Flexible Packaging. One of the nicest aspects of tin can packaging is that it offers a great deal of flexibility. Tin provides excellent strength and stiffness, as well as high packaging flexibility, due to its numerous characteristics. You may easily rearrange these cans in whatever way you desire to transport them across various modes of transportation while maintaining their condition. Other types of cans are more susceptible to deformation.
Disadvantages Of Tin Cans
Acidic Products Packaging. The fundamental disadvantage of tin can packaging is that, unlike any other metallic can, it cannot be utilized to package severely acidic items. It’s because tin is corrosive, and the acidic items’ packaging would almost likely spark a reaction that would destroy both the can and the product. As a result, acidic items should not be stored in tin cans.
Applications Of Tin Cans
- Pharmaceutical Industry
- Food industry
- Cosmetic industry
- Building and construction industry
Aluminum Cans

Aluminum cans are packaging cans that offer the necessary barrier to prevent moisture infiltration and the escape of subtle flavors. It also prevents photo-oxidation, which results in a rancid flavor from fat and oil components in dried food products, which is caused by UV radiation, which is found in most forms of lighting.
Advantages Of Aluminum Cans
- Availability. The most common metal and the third most prevalent material in the Earth’s crust is aluminum. This indicates that there is a plentiful supply of aluminum available for industrial applications such as food packaging, confectionery, and personal care goods.
- Longevity. Even if no maintenance is performed, aluminum packaging can preserve its integrity for a long time. It is also corrosion-resistant, which adds to its long lifespan. As a result, aluminum is an excellent material for food packaging.
- Sustainability in the Environment. Aluminum can be recycled indefinitely, and the recycling process saves a large amount of energy as compared to other materials, using only 5% of the energy used in primary production.
- Versatility. Aluminum is lightweight and has a low melting point, yet it is also exceedingly ductile and easy to form. From a marketing standpoint, this provides aluminum packaging an advantage. Because of the material’s flexibility, it can be easily customized with unique shapes, embossing, and printing for brand recognition and customer appeal. As a result, it’s a popular material for processed food containers, dairy goods, and even pet food.
- Lightweight. Aluminum is a lightweight material that saves money on transportation by allowing more products to be loaded onto vehicles than those bundled with heavier materials. Aluminum may also safeguard the integrity of food products at very thin gauges, reducing the packing material’s weight even more.
Disadvantages Of Aluminum Cans
To prevent aluminum from leaching into the food, aluminum can manufacturers wrap the inside of the cans with a thin layer of plastic. Unfortunately, people may be exposed to hazardous quantities of BPA as a result of using a plastic lining in aluminum cans.
Common Aluminum Can Sizes
While food cans come in standardized numbered sizes, beverage cans, which are predominantly made of aluminum, have common sizes that consumers are familiar with. These sizes often vary by region and beverage type. Some of the most prevalent aluminum can sizes include:
- 8.4 oz (250 ml): Often used for energy drinks like Red Bull or smaller servings of soda.
- 12 oz (355 ml): This is the standard can size for soft drinks (like Coke and Pepsi) and beer in North America. It’s the most widely recognized beverage can.
- 16 oz (473 ml): Known as a “tallboy,” this size is very popular for craft beers and many energy drinks. It offers a larger serving than the standard 12 oz can.
- 19.2 oz (568 ml): Sometimes called a “stovepipe” can, this size is gaining popularity in the craft beer market, especially for single-serve sales at convenience stores.
Applications Of Aluminum Cans
- Food cans
- Beverage cans
- Paint cans
Paper Can
Due to their eco-friendliness, paper and paperboard-based materials are one of the earliest and most widely used packaging forms for food goods such as milk and milk-based products, beverages, dry powders, confectionery, bakery products, and so on.
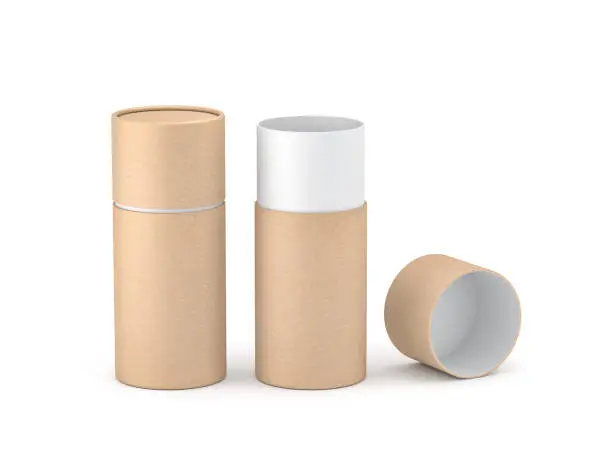
Advantages Of Paper Cans
- Biodegradable Materials. Paper containers are created from renewable resources like paper and paperboard, ensuring that they are environmentally friendly. The raw material, like wood, may be supplied from sustainably managed forests and is easily recyclable and biodegradable by definition.
- Multi-purpose. Paper packaging can be reused as wrapping paper, fiberboard, and paper sacks, among other things. Plastic bags, unlike paper, can only be recycled into more plastic bags. Furthermore, enhanced paper bags enable the storage of dry items on shelves, preserving both the food and the shelving. Bio-based barrier materials could someday replace plastic in many applications, with substantial paper bottles being designed for fizzy beverages and even milk.
- It is More Attractive to Use Paper. When it comes to choosing products depending on their packaging, a lot of consumers prefer paper and cardboard. Paper and cardboard packaging is more appealing to two-thirds of consumers than alternative packaging materials.
- Top-Shelf Solution. A lot of brands benefit from the convenience and visibility of paper product packaging. Aside from that, the packaging benefits include the ease with which different items can perfectly showcase their distinctive packaging and visuals to tell a brand’s story, greater product protection, and stackability.
- High Longevity. Paper bags are both eco-friendly and durable. Heavy loads can be carried in cardboard boxes, which can also stand upright. In addition, progressive paper packing will keep the contents fresh. Paper can lock in odors while keeping pests out, making it a good choice for tightly wrapped items like flour and spices.
Disadvantages Of Paper Cans
Paper packaging has several drawbacks, including low water resistance and inadequate strength in damp conditions.
Applications Of Paper Cans
- Mailing tubes
- Dry Food
- Bakery
- Beverage
Related Post: Metal Cans vs Plastic Bottles for Sustainable Packaging
Types Of Packaging Cans Based On Sizes
Rather than just the volume number, most recipes will state the size of the can. When planning meals in the food service sector, knowing the sizes and capacities of the most common cans on the market is very critical. Many restaurants, cafeterias, daycare centers, and other establishments rely on canned products as a quick and cost-effective way to feed their customers.
Metal cans are measured before seaming on the packers’ end in the United States. These measurements are notional, and while they can be stated in inches, it is more common to adopt a standardized manner of expressing each dimension using three-digit integers.
The first digit represents the number of whole inches in measurement, while the second and third digits represent fractional inches in sixteenths of an inch. The first three digits represent the diameter of the chime measured across the outside of the seam. The can’s overall height is indicated by the second three-digit number. Therefore, 408 x 706 is 4 8/16 x 7 6/16 inches. The following are the types of packaging cans based on size.
Numbered can size | Volume (fl oz) | Volume (cups) | Dimensions (inches, Dia × H) | Description |
#1 (Picnic Can) | 10 ½ -12 ounces | 1¼–1½ cups | 2⅝ × 4 | A small-sized can is ideal for single servings of soup, fruit, or ready-to-eat meals. Convenient for picnics, camping, or lunch boxes. |
#300 | 14–16 oz | 1¾–2 cups | 3 × 4⅜ | One of the most common household can sizes. Frequently used for canned vegetables, beans, sauces, and meats. |
#303 | 16–17 oz | 2 cups | 3⅙ × 4⅜ | Slightly larger than #300, commonly used for canned fruits like peaches and pears, as well as hearty soups or stews. |
#2 | 20 oz | 2½ cups | 3⁷⁄₁₆ × 4⁹⁄₁₆ | Medium-sized can typically used for applesauce, pineapple slices, fruit cocktails, or condensed soups. |
#2½ | 27–29 oz | 3½ cups | 4¹⁄₁₆ × 4¹¹⁄₁₆ | Larger capacity, often used for pumpkin purée, spinach, sauerkraut, or baked beans. Great for recipes serving multiple people. |
#3 | 46–51 oz | 5¾–6½ cups | 4¼ × 4¹⁵⁄₁₆ | A large can used for tomato products (whole, stewed, or sauce), fruit juices, or jams. Common in food prep and institutional use. |
#5 | 56–59 oz | 7–7½ cups | 5¹⁄₁₈ × 5⁵⁄₈ | Typically used for bulk packaging of fruit juices, soups, or vegetables. Suitable for small restaurants or family gatherings. |
#10 | 109–117 oz | 12–13½ cups | 6³⁄₁₆ × 7 | Medium-sized can typically be used for applesauce, pineapple slices, fruit cocktails, or condensed soups. |
Not sure what all those numbers really look like? Check out the size comparison chart below to get a clearer picture.
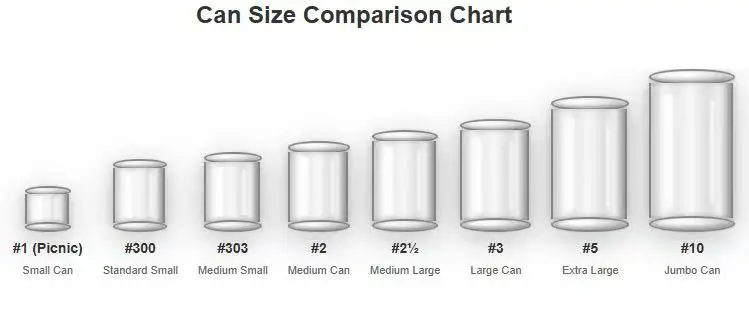
- #300 can.
The #300 can hold approximately 15 ounces and is one of the most frequent sizes in your pantry. The dimensions of these cans are 3″ broad by 4 7/16″ tall. In this size can, you’ll find canned beans, other veggies, and some fruit. This can is about 3″ wide and a bit less than 4″ tall. A #300 can will yield approximately 3 1/2 servings on average. You may come across older recipes that specify #303 cans. They were a tad heavier, but only by a couple of ounces. In most circumstances, the more common #300 cans will suffice. Some items are still packaged in these cans today.
- #10 Can.
Depending on the contents, the #10 can hold over 6 pounds and over 20 servings. This can is approximately 6 3/16″ broad by 7″ tall. These huge cans are more commonly found at Costco or Smart & Final than at the grocery store. This is a pretty large can. If you have a large family, this may be a cost-effective option.
- #303 can.
In a 303 can, there is around 16-17 oz. There will be around 2 cups of this.
- #10 can.
6 pounds 6 ounces, or 96 fluid ounces, which is 12 cups or 3 quarts, is held in a #10 can
- #picnic can.
This can size is equivalent to 10-1/2 to 12 ounces or 1-1/4 cups
- #2 ½ can size.
As shown on the table, this is equivalent to 1 pound 13 ounces or 3-1/2 cups
- #2 can size.
This size can be equated to 1 pound 4 ounces, 1 pint 2 fluid ounces, or 2-1/2 cups.
How To Choose The Right Containers And Machines For Your Production Line

Choosing the right packaging for your new product can make or break its success once it hits the shop shelves. This, of course, has a direct impact on your company’s long-term ability to expand and compete, and it applies whether you are in the natural food, pharmaceutical, or chemical industries.
Despite its importance, choosing the correct packaging for your business needs may be difficult for any manufacturer, even with the number of options presently available. Below are the factors to put into consideration when choosing the right containers and machines for your production line. Read on.
Focus on sustainability. Packaging options must include sustainability, especially if you are selling to the natural food, nutraceutical, or body care businesses. At the very least, seek recyclable packaging: this will make your customers pleased and give your company a greener, more environmentally concerned image. Consumers today don’t want Styrofoam!
Stick to standard sizes and shapes. Stick to common forms and sizes that packaging makers can easily produce to save money. While distinctive forms and sizes can assist in capturing people’s attention in the store, the extra cost and problems of packaging manufacture aren’t worth it.
Standard forms and sizes can provide you with more flexibility and ease when it comes to storage, handling, and transportation. By avoiding specialized packaging alternatives, you may be able to place smaller orders and save money. Instead, put those savings toward smart design decisions that can improve your brand’s visual impact and awareness.
Staff Training. The quantity of training, education level, and staff hours required to run the machine will all be influenced by the machine type you choose. An automatic filling machine, for example, will require significantly more training than a semi-automatic filling machine.
Someone must keep the infeed conveyor full of empty pouches on a Premade Pouch Machine. The operator, on the other hand, is free to focus on other corporate responsibilities after the automatic filling machine is configured. Automatic splicing for film and zippers, as well as end-of-line case packaging systems, are two possibilities for reducing downtime and increasing output. PPI Technologies Group offers various training options for the equipment you purchase, helping to set you and your team up for success.
Excellent branding and design. Invest in excellent packaging design, both in terms of materials and visuals. The materials you use for your packaging might help to reflect your brand’s identity. Select materials and an overall design that appeal to your target market and can be applied across multiple product lines.
Your packaging should coordinate with your logo and the rest of your product range. Brand packaging design can help you increase sales and enhance your bottom line by sending the proper message. Choosing the right size and material of containers allows you to display your packaging design perfectly.
Speed. What machine you should select depends on how quickly and how much product you plan to produce each day. If this is your first purchase of filling and sealing machines, you may not need to go for the big guns just yet. Don’t be scared by the fact that larger isn’t necessarily better. Begin where you can and give yourself time to develop.
The fastest accessible packaging option is automatic can packaging machines. The Premade Pouch Machine, on the other hand, is gaining popularity in the packaging industry due to its versatility. Because both machines offer advantages, your choice should be based on the desired production speed, labor, and SKU diversity.
Your Expert Partner in Can Packaging Solutions: Levapack
After exploring the diverse world of packaging cans, partnering with a reliable equipment manufacturer is the final step to ensuring your production line’s success. Since 2008, Levapack has been a trusted partner for food producers and packaging machinery distributors in over 100 countries. We don’t just sell machines; we deliver complete, customized automation solutions.
Whether you’re packaging powders, liquids, or solids into tinplate, aluminum, paper, or plastic cans, our expert engineering team can design the optimal filling, seaming, and labeling line for your needs. Our equipment is built with high-quality 304/316 food-grade stainless steel and premium electrical components from world-renowned brands like Siemens and Schneider, all certified by CE, ISO, and CSA to guarantee exceptional stability and durability.
Our robust supply chain and 4000㎡ factory enable us to deliver standard machines in as fast as 1-7 days. From initial consultation and line layout design to our extended 16-month warranty and 7/24 global after-sales support, Levapack is committed to being the backbone of your success.
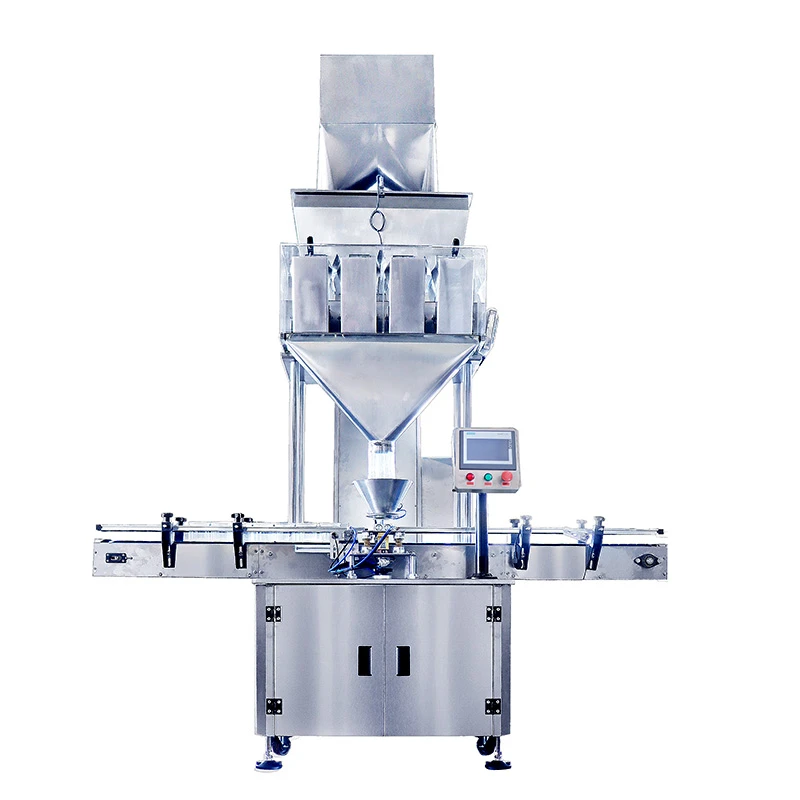
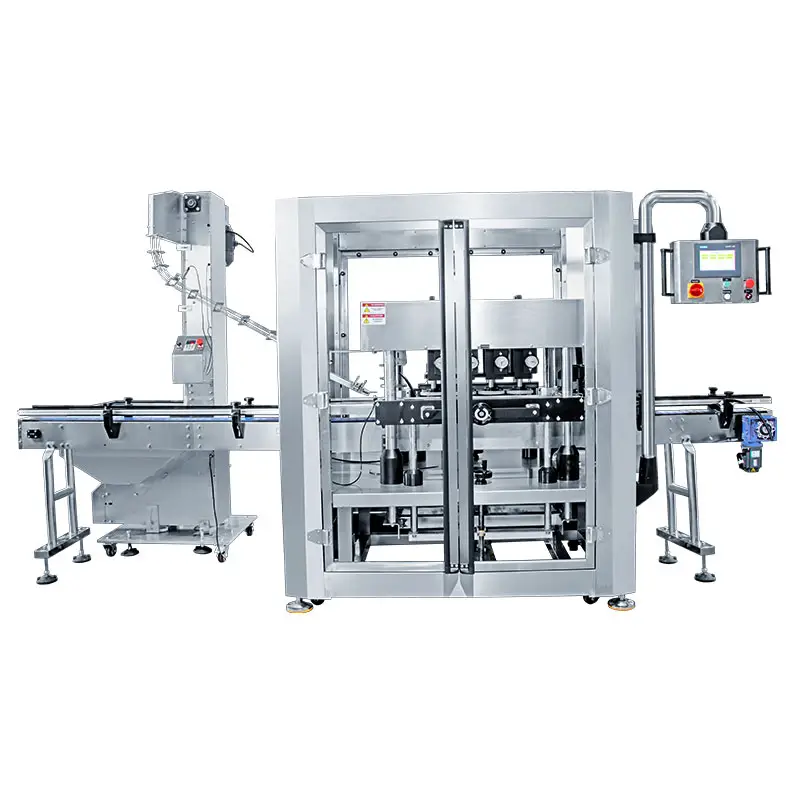
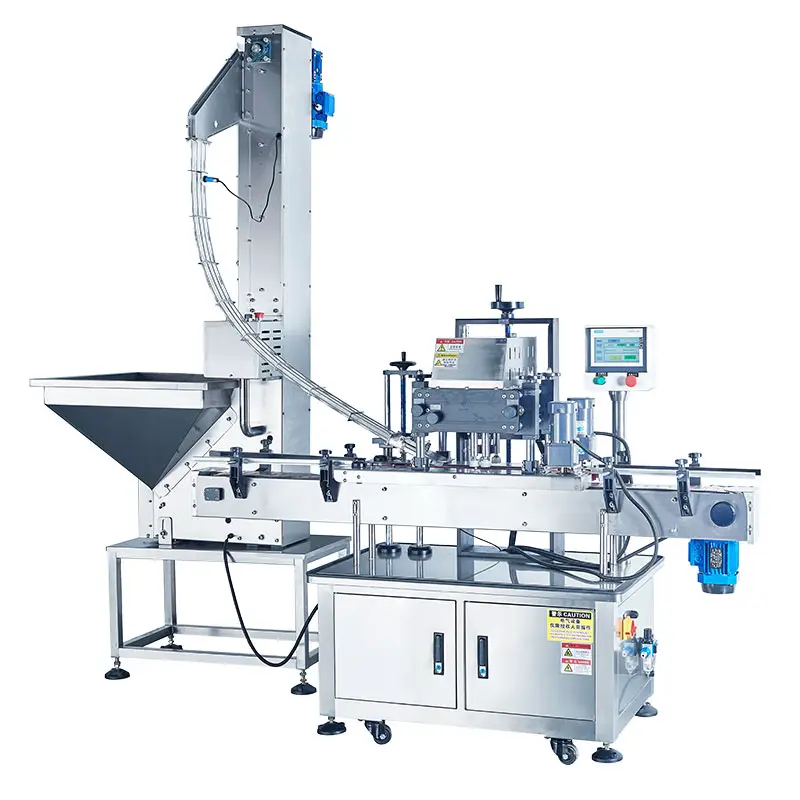
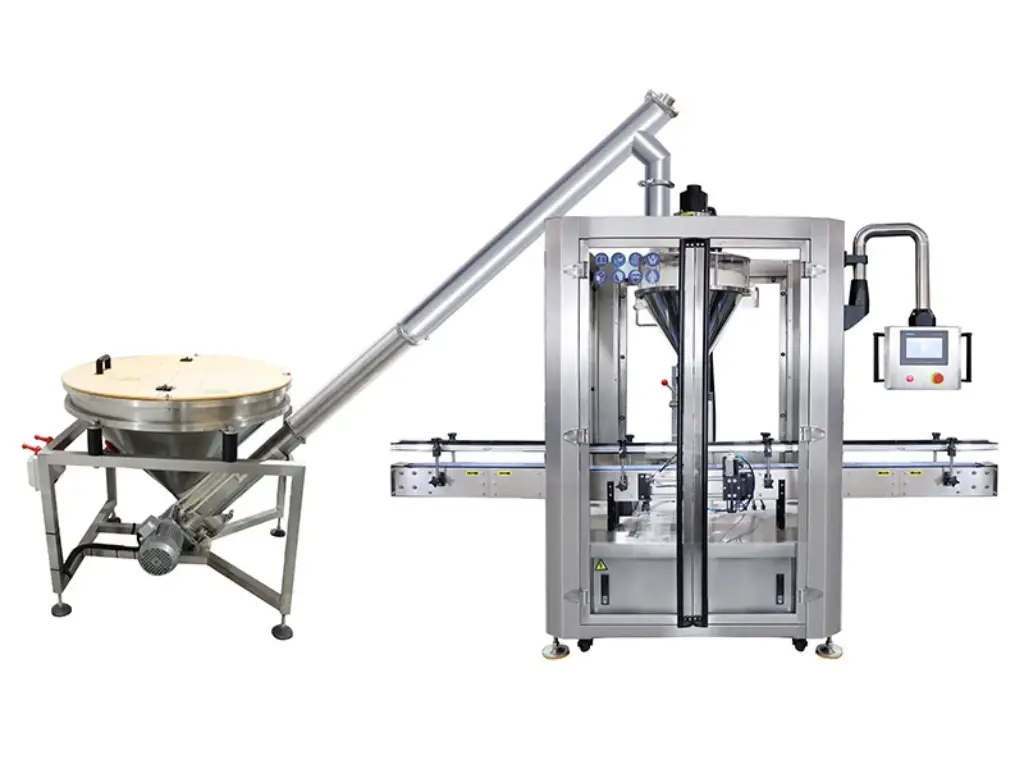
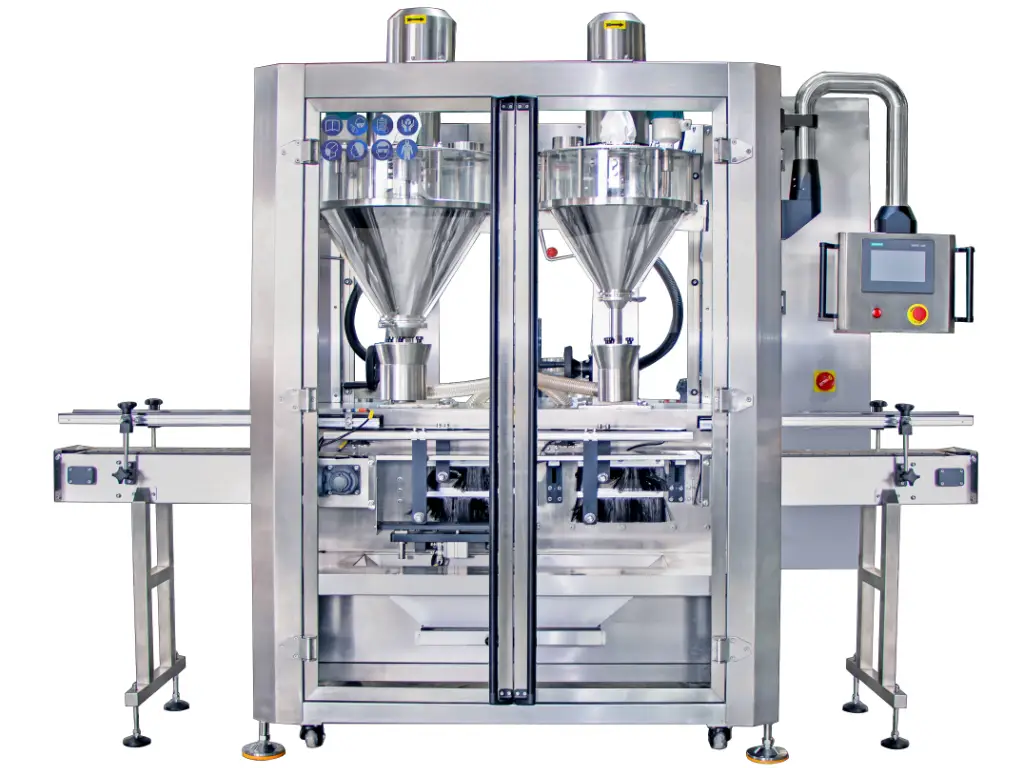
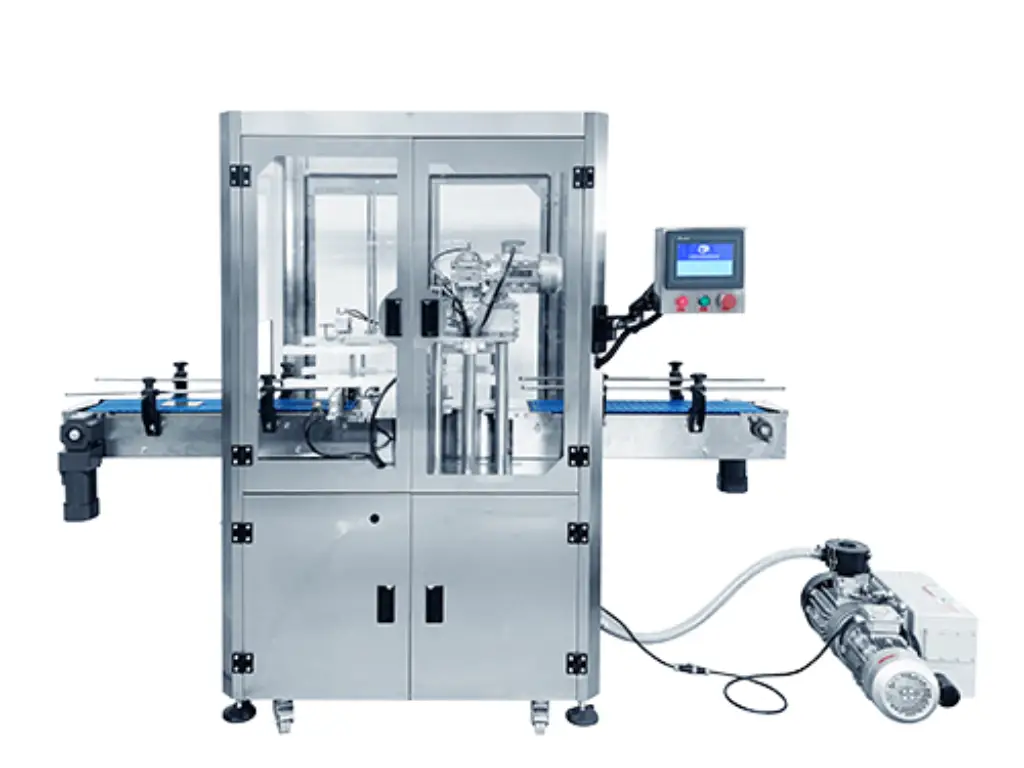
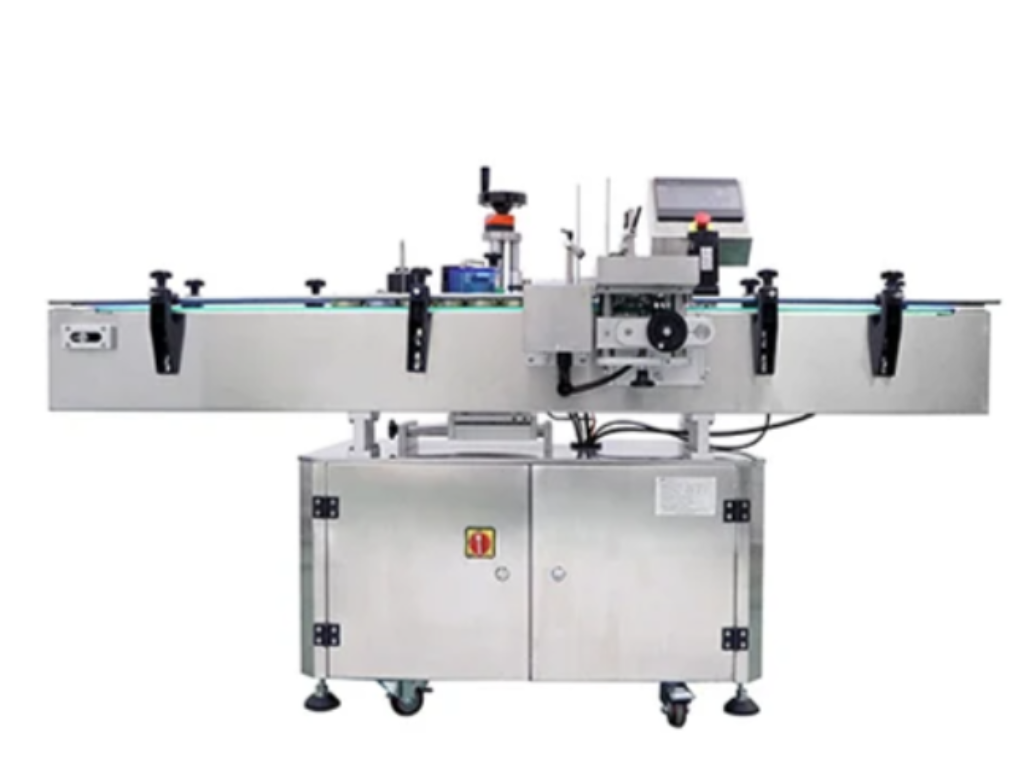
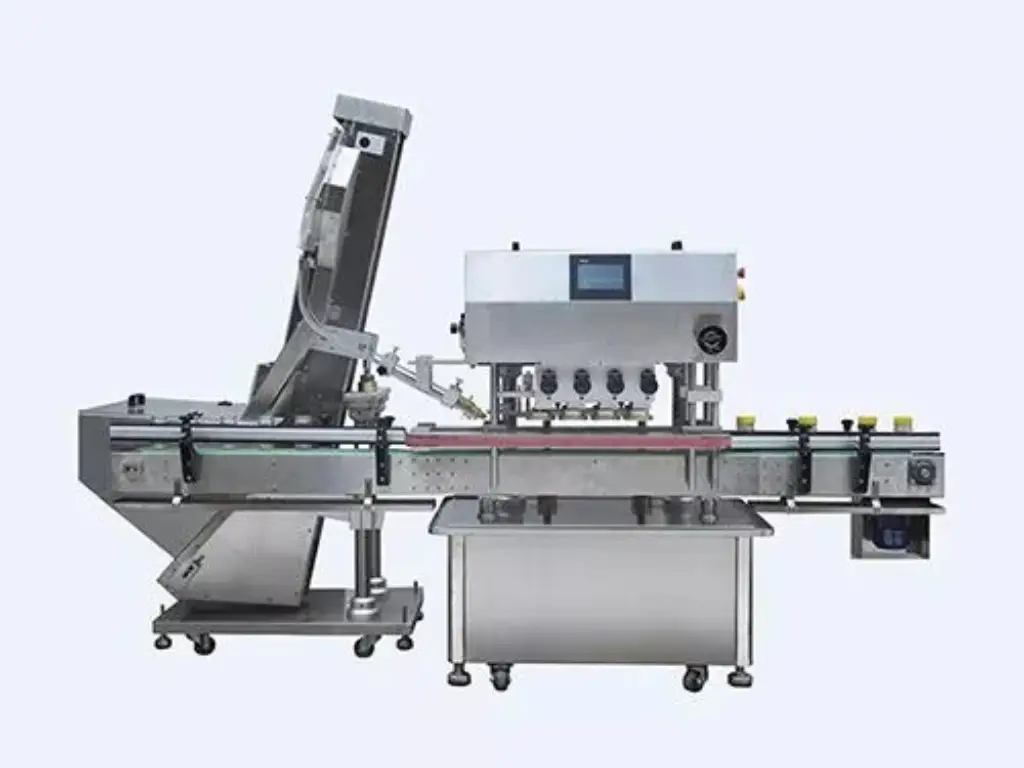
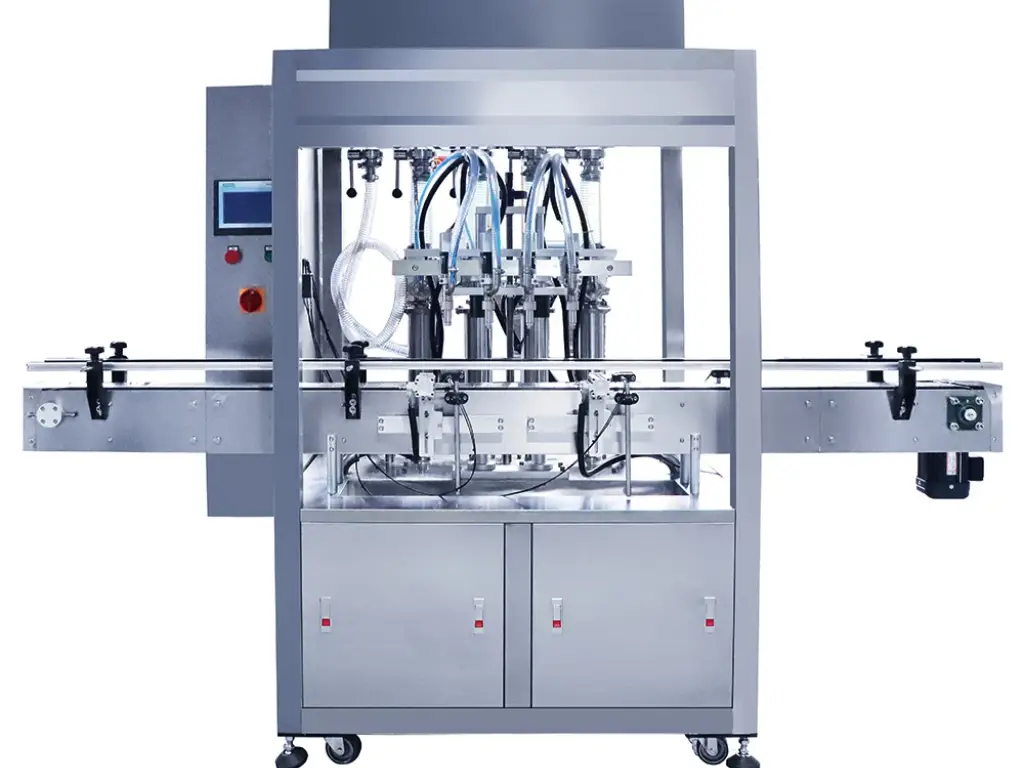
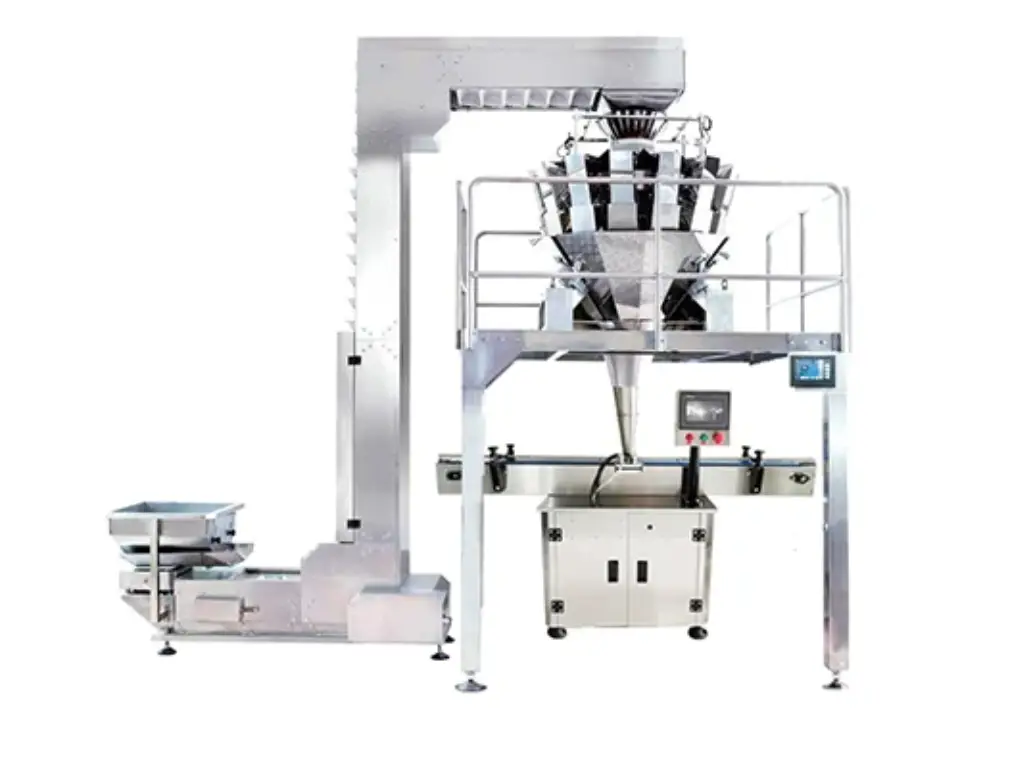
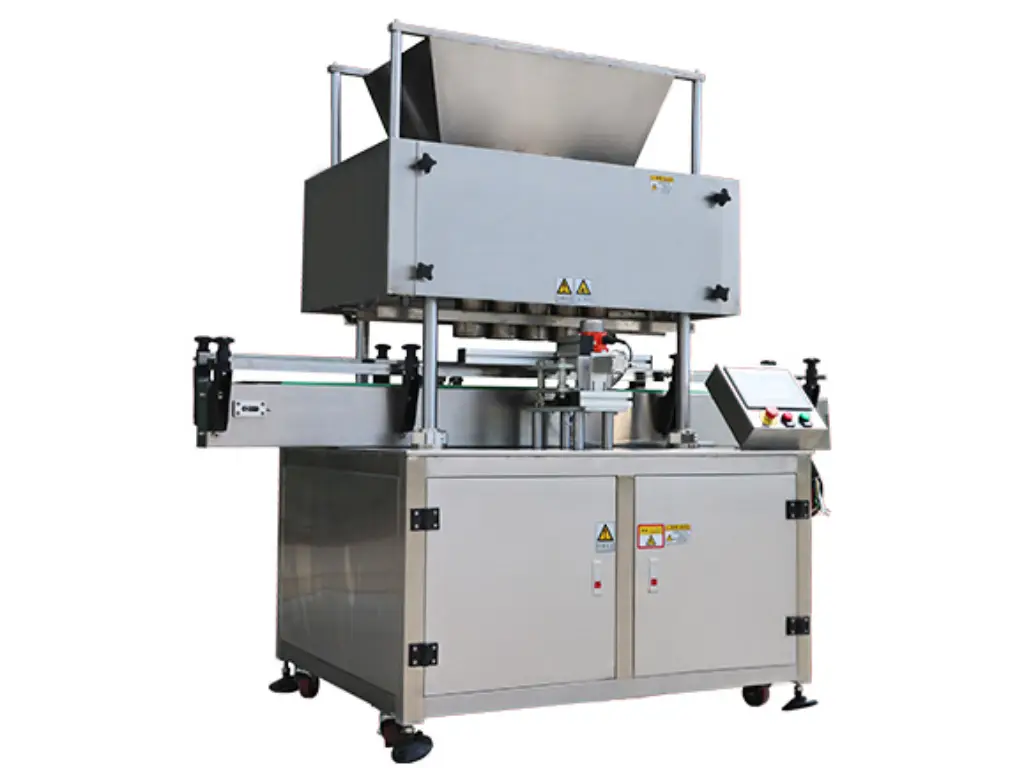
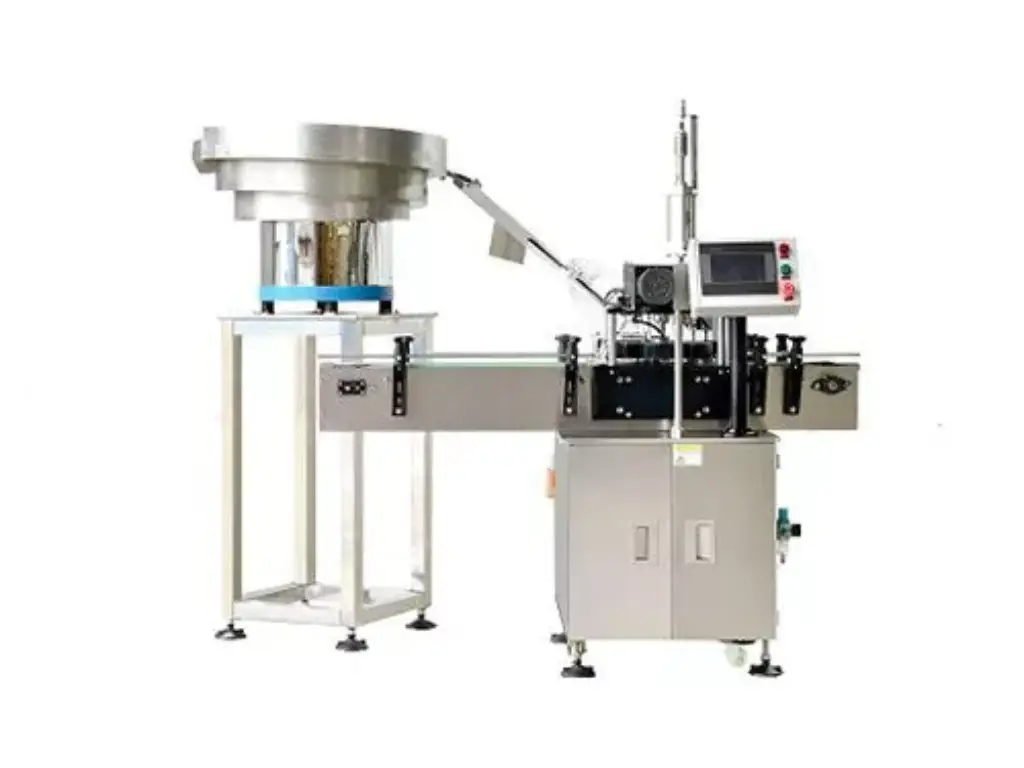
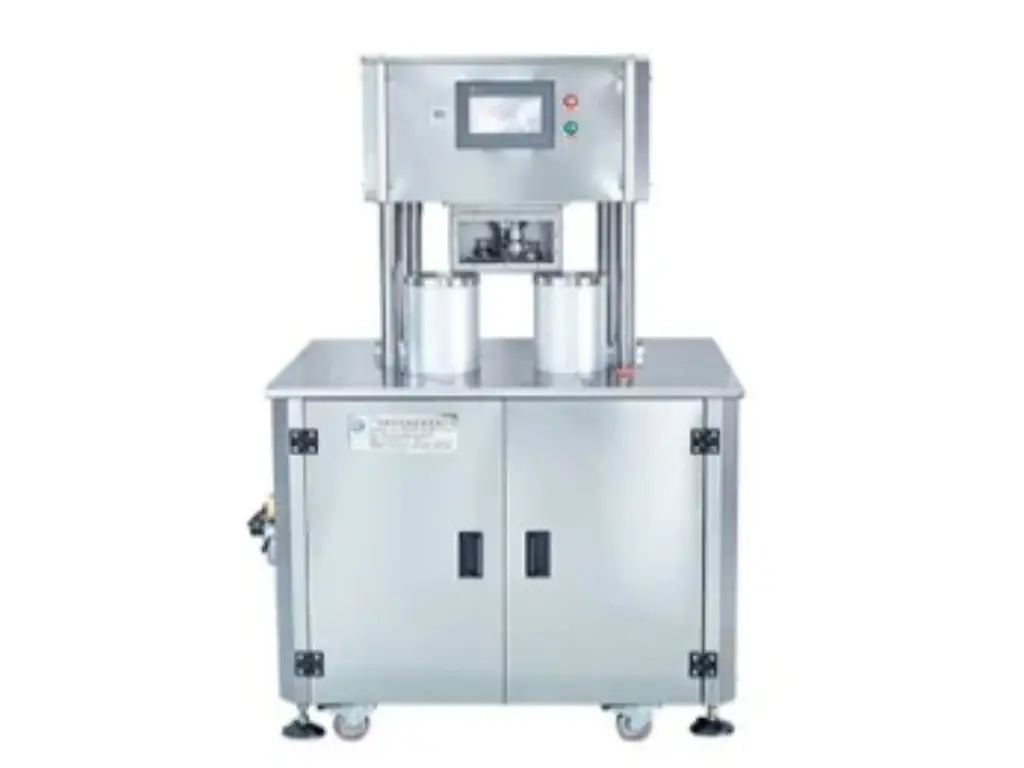
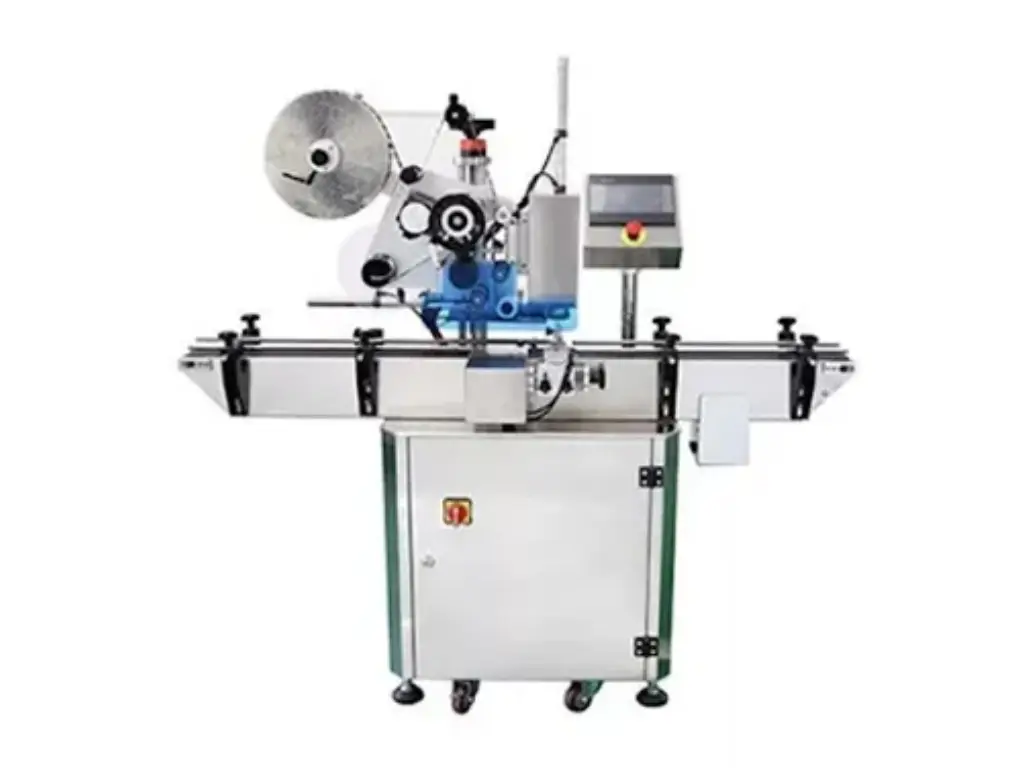

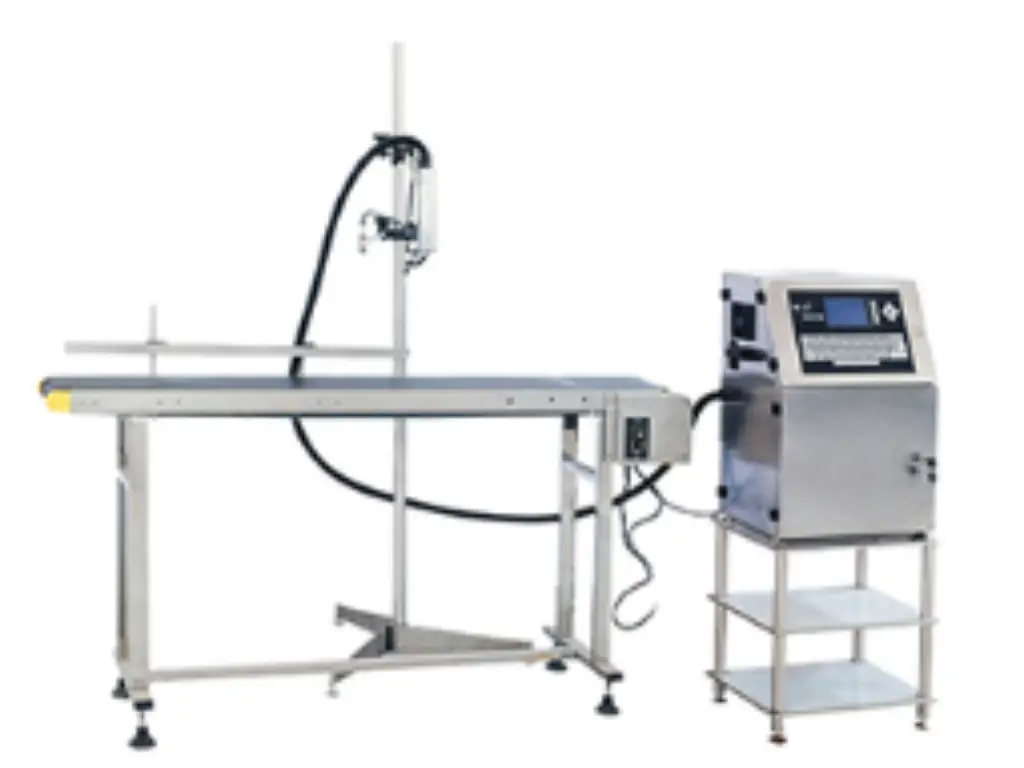
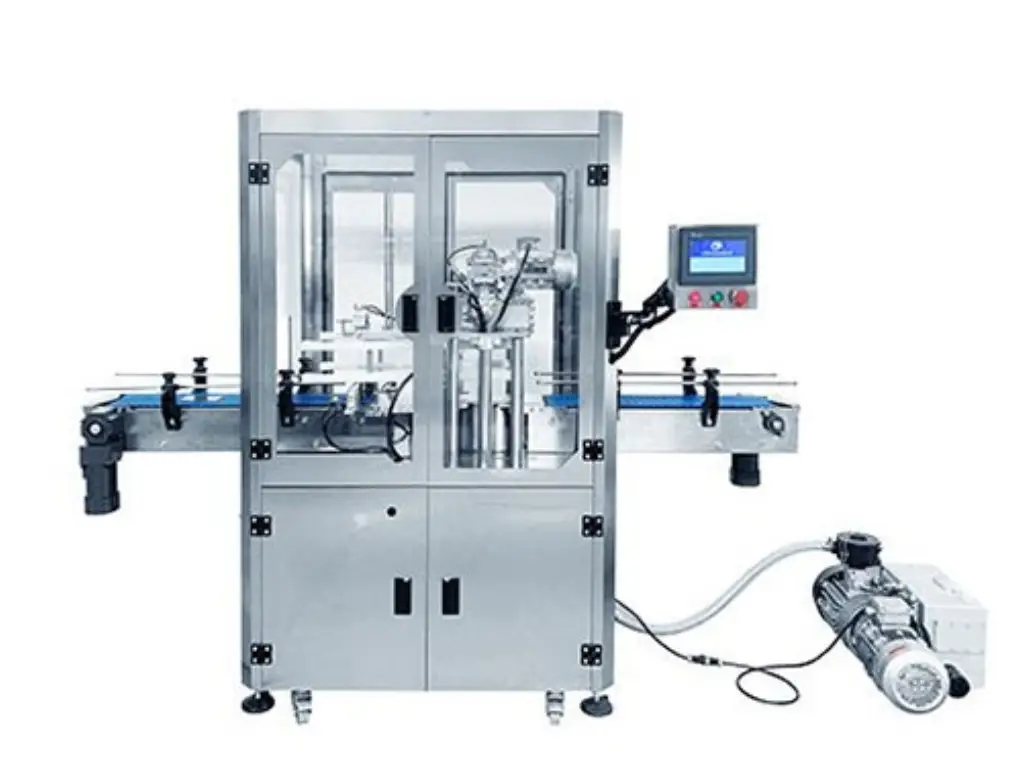

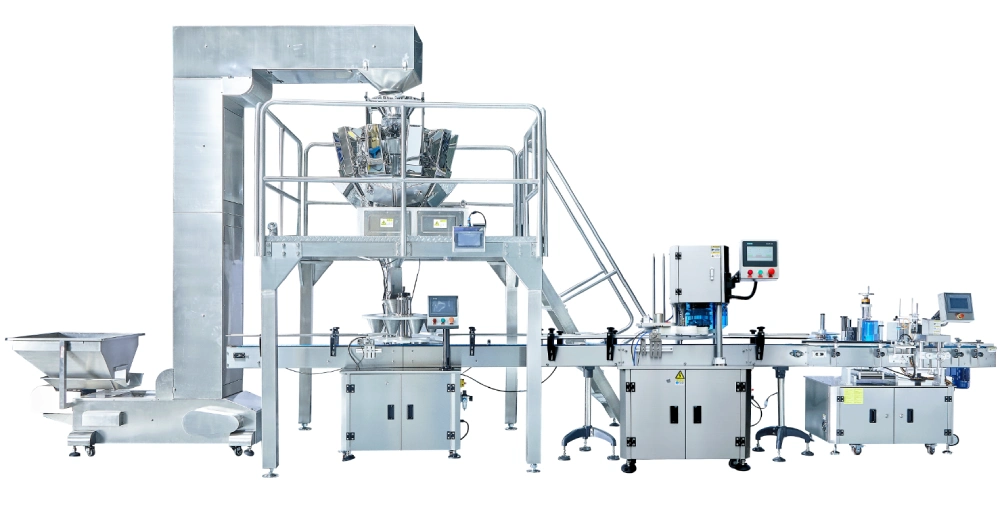

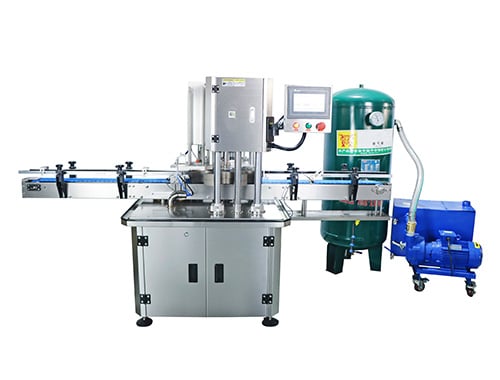
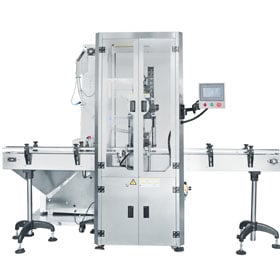
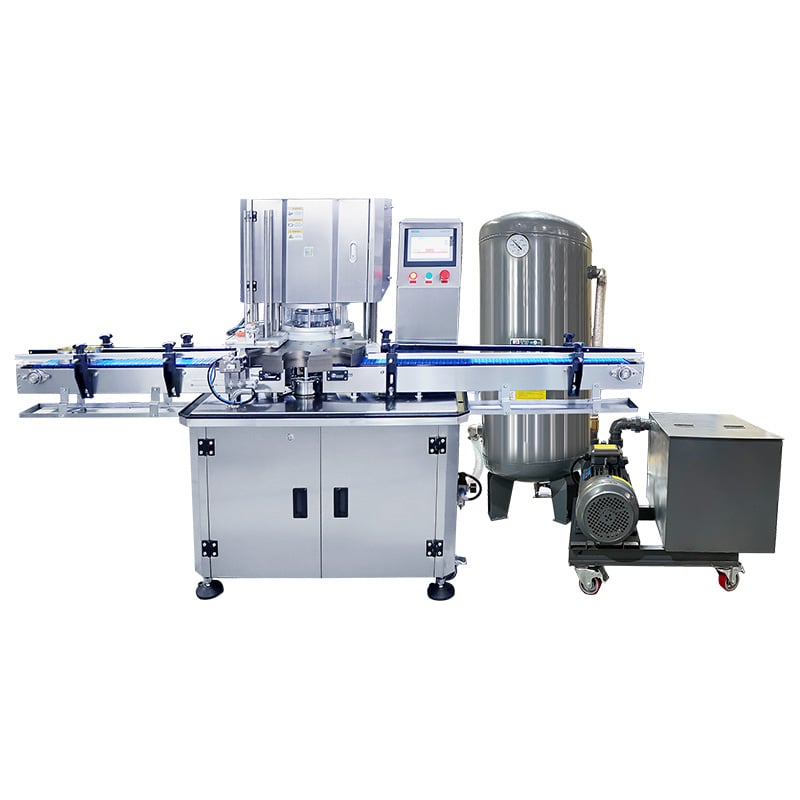
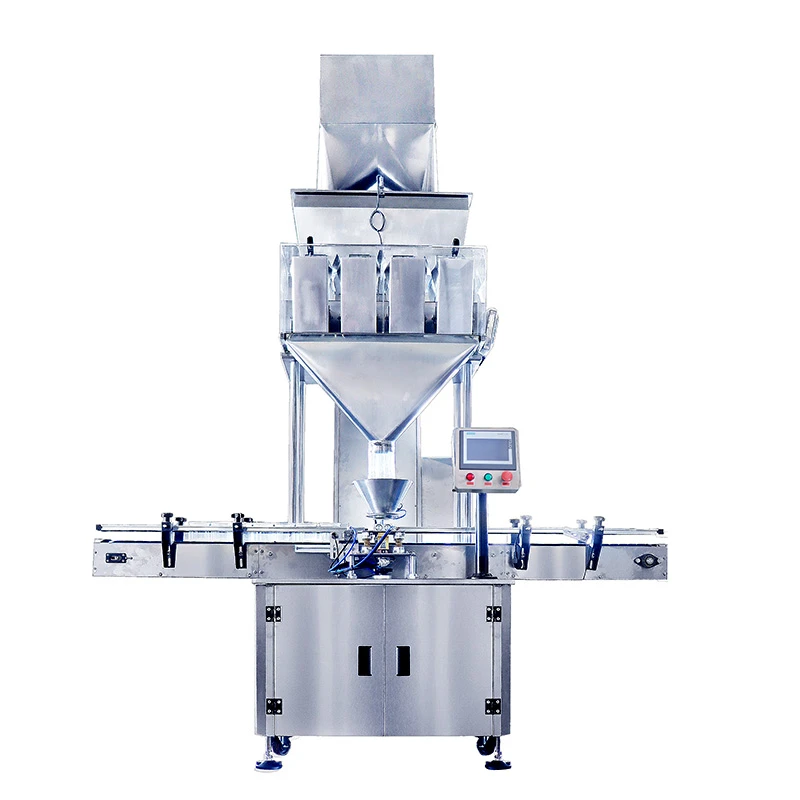
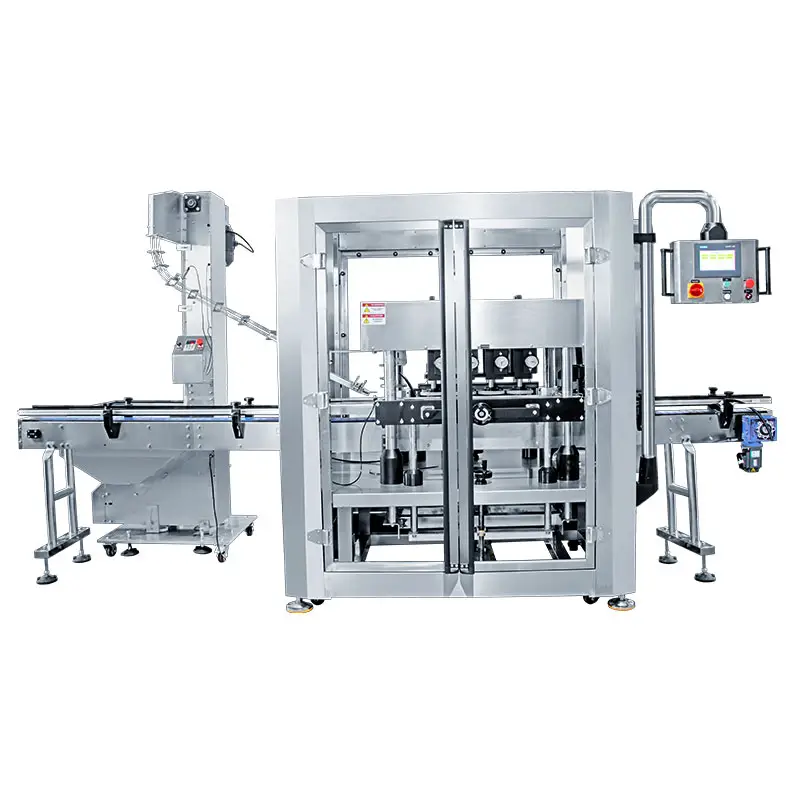
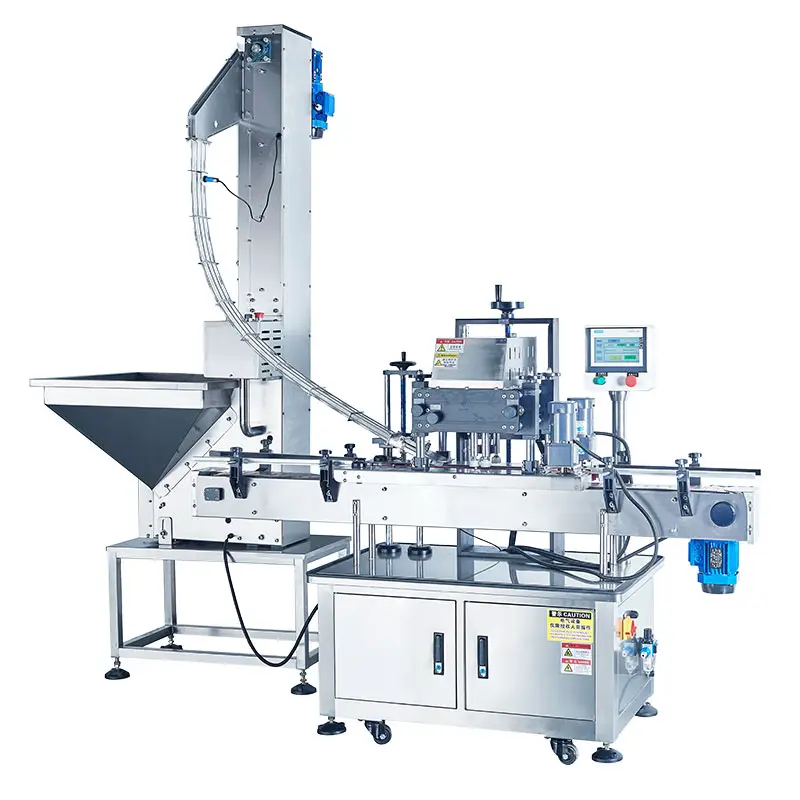
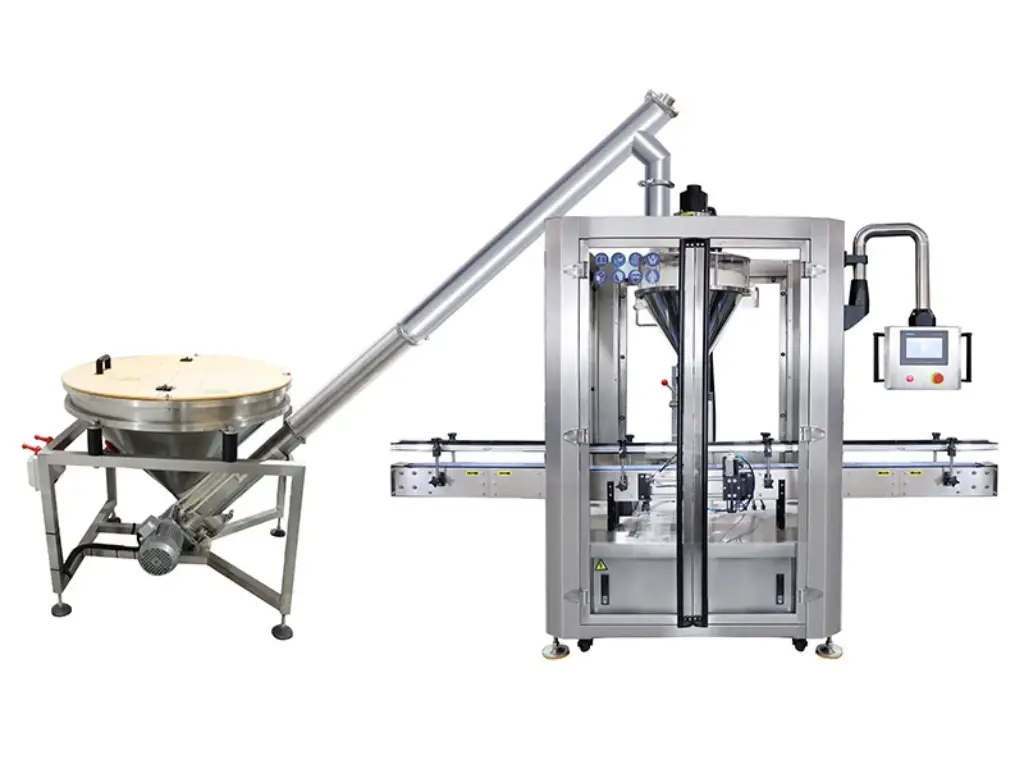
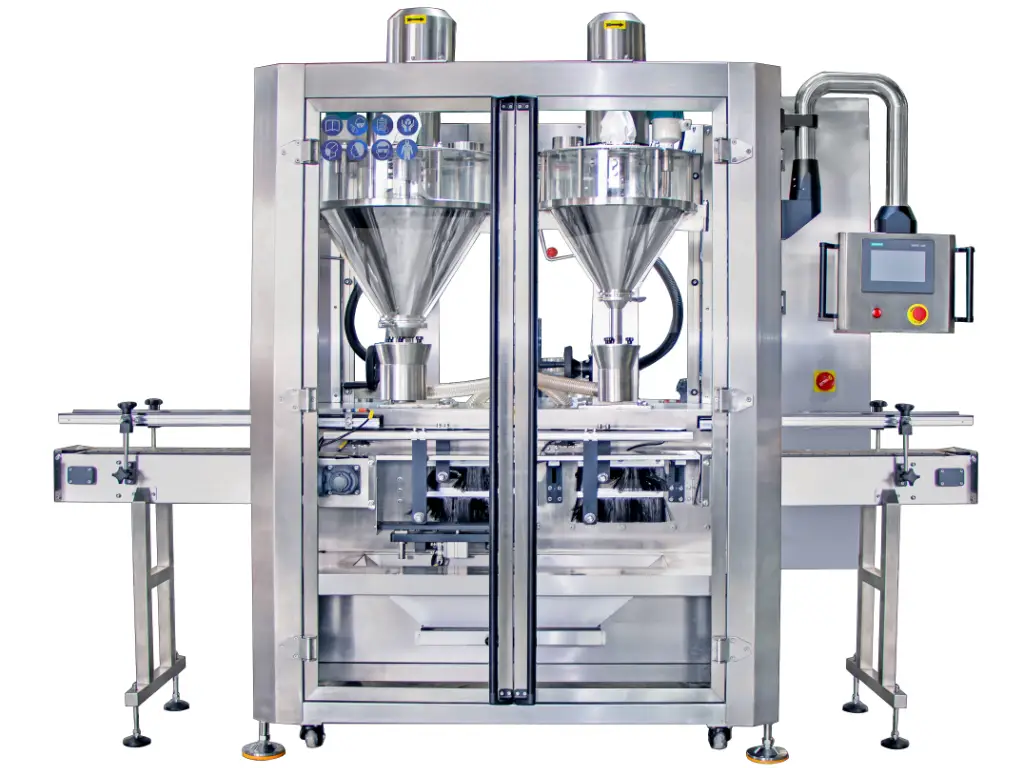
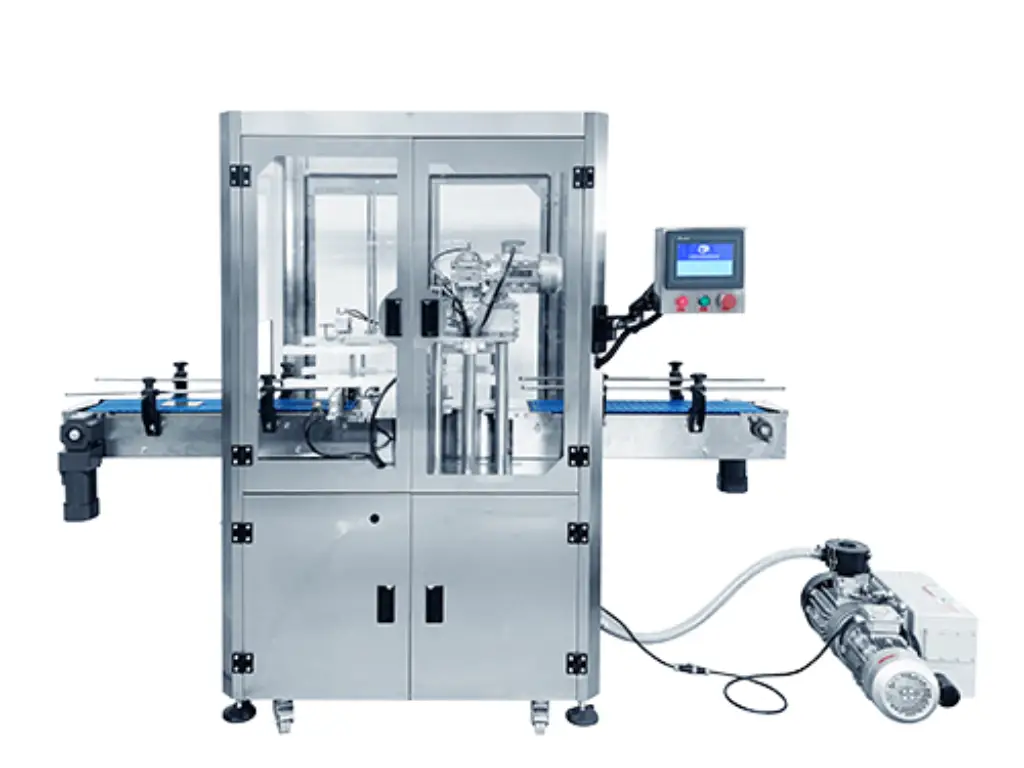
Conclusion
Generally, packaging cans are any sort of packets, envelopes, or structures that are meant to protect and advertise various items. Between manufacturing, distribution, and labeling, your commodity’s packaging should be able to safeguard it from contamination and harm. Contact us for any inquiries or to order affordable and high-quality packaging cans.
FAQs about Packaging Cans
Most packaging cans are made from aluminum, tin-plated steel, or zinc-plated steel. Thanks to these materials, the product inside is protected from light, oxygen, and moisture, and it stays safe for a long time.
Most Coke cans are made from light aluminum, which does not rust and is easy to recycle. Most beverages are sold in aluminum cans because they help keep the drink fresh and are environmentally friendly.
Most soda cans are made from aluminum, which is light, affordable, and easy to recycle. That’s why aluminum is often used to make and distribute carbonated drinks in large quantities.
Some soup cans are not made of aluminum. Although some soup cans are aluminum, most are made from steel that has been coated with tin or zinc. Steel makes the containers stronger and more rigid, which is important for heavier products such as soups and stews.
No, aluminum and tin are different metals. Aluminum is a metal that is light and does not rust, while tin is commonly used to coat steel (tinplate) to prevent it from rusting. Beverage cans are usually made of aluminum, while tin-coated steel is the main material for food cans.
Many packaging cans are recyclable since both aluminum and steel are easily recovered. Recycling aluminum cans uses less energy than making them from scratch, and the recycled cans can be used to make new things, saving natural resources. New steel products can be created from recycled steel cans.
The plastic coating inside most aluminum cans is there to prevent the aluminum from reacting with the food or drink and to keep the product tasting good. Because of the plastic coating, aluminum does not corrode with acidic liquids, and the product lasts longer.
The length of time canned foods are good for depends on their type. Usually, canned vegetables and soups are good for 6 months to 1 year, but canned meats can be kept for 2 years or more. The time foods can be stored depends on temperature, humidity, and how well they are sealed. Most canned foods stay fresh and nutritious if they are well sealed.